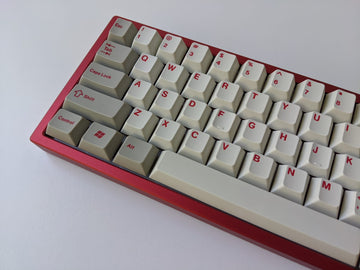
The Beginning
This project was the first in a series I started in March 2020. The available options at the time were very different to what it is now at the time of writing (Jan 2022). And even more different now as I revisit what I've written! (Jan 2023). And even more more different as I re-revisit what I've written (Jan 2024)!!! So let's cast our minds back to 2020 in the thick of COVID. There was a huge boom in growth in the community and demand increased while readily available supply was already limited. However, the global pandemic only further complicated matters and made it increasingly difficult for beginners to source budget friendly options.
With so many newcomers entering the scene, at the time I had envisioned having another option for a beginner friendly board readily available in the Australian community. At the time, not only was there limited supply but also limited diversity in options, namely tray mount designs. This refers to the style of assembly of the keyboard. A quick Google search for "custom keyboard mounts" will yield a great cheat sheet for understanding basic differences.
The intentions were simple for my first project:
- Non-tray mount design (I opted for bottom mount)
- Lower manufacturing cost with design simplicity
- ANSI layout
- Hotswap
- In-stock
I believe that ANSI is a more familiar layout for newcomers to the custom keyboard scene. It was typically easier to buy any keycap sets with compatibility for ANSI but these days it's less of an issue. In addition, hotswap would be easier and more cost effective so there's no need don't to buy additional equipment for soldering.
The Middle
Why bottom mount?
I didn't see too many designs with bottom mount at the time of brainstorming ideas. Top mount and gasket mount seemed to largely dominate. (Even to this day I haven't seen many bottom mounts - Jan 2023). The difference between top and bottom mount is which half of the case the plate is fixed to. The direction of keypresses force plates in a downwards motion. As such, one of the main differences between the orientation of top and bottom mount is part of the surface area of the case that provides additional support to the plate with bottom mount. Whereas for top mount, the plate naturally moves away from the case it is fixed to and therefore has a little more deflection, assuming that other variables are held constant (such as the plate material, thickness, how the mounting points are positioned and designed and so on). I felt that this in theory shouldn't make that significant of a difference between the two and seemed like a good opportunity to do something slightly different to what was trending.
I felt that bottom mount could focus the majority of manufacturing complexity on the bottom case piece while the top piece could be a thin section to cover up the mounting locations. This in turn would help with the goal of lowering manufacturing cost.
In addition, by focusing the design complexity into the bottom case, more mass would be in the bottom piece which the plate would be fixed to and this in theory would help reduce vibration of the case as opposed to a thinner and lighter design. The cavity was kept to a minimum with the intention of reducing reverberation.
I wanted to minimise cuts to the plate as much as possible. I didn't intend for the design to be tailored for flex as this would require an increase to cavity height, which would affect the reverberation. Additional cuts also introduce airborne noise flanking transmission paths. This further complicates the design, potentially requiring more features to help reduce reverberation and noise transmission, which moves further away from the intent of minimising cost and creating a board targeted more towards newer hobbyists.
Why not support multiple layouts?
I wanted to minimise cuts to reduce flanking paths. Also, the mounting point locations become less intentional. This may reduce some of the consistency in feel and sound. For example, a mounting point intended for a 6.25u spacebar, which then also allows for 7u support, would then become off-centred. ANSI was the priority for this design to be more suited to newcomers as it's a layout many are familiar with and extra safe with keycap options. To allow for layout compatibility, the PCB would also need to be solderable which moves away from the more beginner friendly hotswap. Either that, or multiple hotswap PCB layouts are required, which can become costly to supply.
Mounting Points
The mounting point underneath the spacebar is divisive due to the added stiffness and loudness. I'm of the opinion it's a preference as to whether people find they like it or not, with a large majority of more experienced enthusiasts preferring soft and deeper spacebars.
In the R1 prototype, I had an aluminium plate manufactured which only had 4 mounting points, one at each corner. This didn't provide enough support central to the board which caused some bottoming out issues and plate rattling. I toyed with the idea of 8 mounting points but preferred the 6 mounting points to keep things simple (albeit minimally) and reducing the overall stiffness of the typing experience in the absence of any flex cuts, particularly as I was initially intending to offer aluminium as the only plate material.
Aluminium plates were for quite a while a bit of a default, vanilla, safe option. Based on 6 points I placed one under the spacebar directly to hopefully achieve a uniform profile across the spacebar itself, knowing it would also be divisive given the meta in the design world. In my mind, a board intended for newer custom keyboard users meant that they also wouldn't have much background context for what was in meta as well as not yet understanding what their preferences may be. Meanwhile, experienced users who know they don't like a stiff and loud spacebar would steer clear of the board, leaving more leftover for newer users! Did I mention I wanted this to be an in-stock, boring but safe board at a price hopefully easy to swallow enough for a newer user?
R1 Prototype
This was completed in July 2020.
One issue that came up was that Durock stabilizers, which became heavily popular around that time, actually had slightly wider housings than what was considered the market norm then. They were extremely difficult to fit through the plate.
Secondly, the air cavity was very short, which was intentional, but given the rising popularity of flex and bounce, I had concerns for users modifying their boards in a way that could cause bottoming out issues of the PCB. This might look like o-ring modifications or having their own plates cut as half plates or softer materials. As such I wanted to revert back to what was more of a standard shallow cavity height rather than being too extreme.
The USB port was an enlarged ugly cut-out and this was due to not having any PCB file to work with. Being an absolute noob when it came to PCBs I thought at the time the enlarged hole would also mean safety in PCB port compatibility in case anyone wanted to BYO 60% ANSI PCBs to the case and plate.
After learning more from some much smarter and experienced community members that many 60% PCBs have a similar port alignment, I aimed to change the port cut-out to something with a tighter fit.
R2 E-White Prototypes
SwitchKeys ran 20 units in December 2020 and landed April-May 2021. The main changes were the plate stabilizer cut-outs and increased cavity height for safety. It still had the regular 3M bumpons for feet and enlarged USB port.
R3 Prototype
This was completed in May 2021.
In January 2021 I was provided with a PCB file I could model the USB cut-out with peace of mind against. The R3 prototype changes included an additional two case screws to try reduce risk of light bleeding through the seam if people chose to use a PCB with RGB, different feet cut-outs, USB receptacle clearance in the bottom case to assist with dropping the plate and PCB into place, and this resulted in shifting the mounting point at the USB port over slightly.
I felt like the case and plate design were at a stage ready for production though the need for such a board in the market was nowhere near as urgent anymore with a plethora of budget friendly entry-level boards made available towards the end of 2020 and early 2021. However, a PCB to go with the kit was constantly a delaying factor to the project.
The End?
As of January 2022 the case and plate is ready to produce with the only change from the R3 Prototype being feet cut-outs to suit the AEBoards Feet. An R1 PCB prototype run was completed late 2021 and an R2 PCB prototype competed January 2022, with the main change fixing the caps lock LED indicator.
The main limitation with the design of the HH60 Seamed is the colour options due to the thin top piece. While it assists with lowering the manufacturing cost significantly, it also poses a risk of anodization mismatching. To date, seven different colours have been manufactured in prototypes for this design: E-white, black, red, blue, tiffany blue, purple and grey. The grey was the only one with noticeable mismatching.
As such the conclusion from Dadesin (the CNC manufacturer) was that brighter vibrant colours posed the least risk for mismatching with this type of design which would govern the colour options made available.
Aside from the E-White limited run that SwitchKeys did, this style of ANSI with the thin top case never went ahead into production. Instead the seamless variant was manufactured which is what the HH60 is now.
A New Beginning
From the R2 E-White Prototypes there was feedback from a few who wanteed the HH60 seamed to support a 7u layout or to remove the ANSI layout altogether, though the sample crowd were mainly existing enthusiasts rather than beginners to the hobby. I didn't want to incorporate both layouts for the aforementioned reasons discussing layouts and felt like removing ANSI was moving away from the design being catered towards more for beginners which was the initial intent.
This became the beginning of the design of the HH60 in its current form. It was actually the third design, after the HH60 Seamed (the OG) and also prototype designs were made for a HH-Full (a full-size ANSI hotswap). The original idea was to have a 60%, TKL and Full-size line-up with all the same design language as a family of keyboards. This initially looked like bottom mount keyboards, all with seamed finishes to lower cost, and all ANSI hotswap. But as mentioned before, there was a major limitation in the anodization matching using such significantly different thickness pieces.
From the HH-Full R1 prototype, this was more prevalent than for the HH60 Seamed due to the rear of the board being even thicker than a 60% form factor. As such the HH-Full R2 prototype was going to be changed to a seamless finish, but this would increase manufacturing cost significantly and did not seem to fit the bill of being a budget and beginner-friendly price point anymore. With that in mind, the HH-Full was changed to a 7u bottom row layout as well. And so, with the feedback of wanting the HH60 to support 7u bottom row layout, this became a good opportunity to make a separate 60% to match the design language of the HH-Full R2 prototype.
The Middle Again
Mounting Points
8 mounting points were used to keep the mounting points away from directly under the spacebar and the 7u layout made it easy to maintain symmetry. In addition, some flex cuts were made only around the spacebar. This style for a softer and quieter spacebar has also typically been more popular in designs, and would be a main point of difference between a slightly more enthusiast focused designed in the HH60 Seamless versus the more newcomer focus of the HH60 Seamed.
R1 Prototype
This was received in June 2021. The main finding that required changing was the clearance of the top case to the screw heads fixing down the plate and this was because the manufacturer had moved away from flat head screws since the HH60 Seamed prototypes were conducted.
There was very little risk of things going wrong with the seamless prototyping phase due to three runs already having been conducted with the seamed design.
Production
Production run for the cases and plates commenced in September 2021 and completed June 2022. Unfortunately around this period, Dadesin (who have a long history of manufacturing custom mechanical keyboards) switched to conducting their own anodization in-house and went through a lot of teething issues. During my quality checks I found a lot of minor issues mostly noticeable under harsh light and generally underneath the keyboards which would not be seen during normal operation. However, it took a very long time to sort through everything to assign as A-stock and B-stock.
The PCBs meanwhile had an issue with the capslock LED light. This took quite a while to find a workaround and update the JSON and bin files.
Unfortunately for Hong Hobbies, by the time everything was well and truly packaged and ready to go, it was already well into 2023 and the hobby had moved on. Fortunately for the community, there have been so many offerings particularly at lower price points for beginners to the hobby. Although there are far less switches available locally in Australia, there appears to be a lot more stock held of highly sought after keycaps which once upon a time you would minimally be waiting 12 months for a set or paying high aftermarket prices. The custom keyboard market has also forced more mainstream manufacturers into making better products which has overall lifted the quality of keyboards.
Final Thoughts
I believe I successfully created a keyboard using my mechanical engineering and acoustic background and have learnt a whole heap more about manufacturing. I hope that people can enjoy the HH60 for what it is being a minimalistic yet acoustically pleasing keyboard.